What is EPMD Roofing?
- John@LiteHouse
- Dec 15, 2022
- 5 min read
Updated: Aug 22, 2023
EPDM (ethylene propylene diene monomer) is a synthetic rubber membrane with elastic properties that is commonly used to cover low-slope roofs on both residential and commercial buildings. Its manufacture involves the use of cross-linked polymers to improve elasticity, strength and durability.

Polymers are custom designed molecules. Cross-linked molecules are those that bond at the atomic level, greatly increasing their strength and durability. The polymer industry generally includes many products in addition to roofing materials. In the U.S. alone, sales of such products are worth more than $425 billion annually.
EPDM is produced by a number of different manufacturers. It is commonly available in thicknesses from 45 mil to 60 mil and may or may not be reinforced. At least one manufacturer offers it in sheets up to 100 feet long and 50 feet wide, although the standard width is usually 10 feet. Larger sheets are an advantage because the roof will have fewer seams, which are potential leak points.
Other potential points of leakage are penetrations, roof edges and joints such as end walls and side walls. For mechanically fastened systems, fastener penetrations are also potential points of leakage.
EPDM typically has a permeability value of 1 or less, making it a moisture barrier instead of a moisture retarder.
EPDM is known as a single-ply roofing system because it is a single membrane, as opposed to an assembled membrane consisting of multiple layers bonded together.
Some of the main advantages of EPDM are its excellent resistance to heat, ozone and weather damage. Compared to other systems used for similar purposes, EPDM performs particularly well in cold weather.
EPDM can be installed in one of three ways:
fully bonded, in which the membrane is fixed with contact cement. This is the preferred method of membrane installation. Fully adherent membranes prevent bloat. A ripple is a stretching and separation from the substrate, usually due to being lifted or blown by wind;
mechanically attached, in which fasteners similar to plastic covers are used to secure the edge of each layer before overlapping and sealing the next layer. The mechanical fastening allows some inflation of the membrane. The degree of heave will depend on the spacing of the fasteners and the pressure difference between the interior of the building and the exterior surface of the roof; and
gravel, in which an aggregate such as gravel, generally called ballast, is installed on top of the membrane. Aggregate is typically ¾-inch to 1½ inches in diameter (#3 or #4 stone). The EPDM membrane is held in place by the weight of the ballast. The advantage of the ballast is that it allows the diaphragm to expand and contract.
Load bearing systems also typically use larger sheet metal with factory-made seams that are superior to field seams.
The downside to ballast is that such systems are heavy -- 10 to 12 pounds per square foot -- and have limited wind resistance.
EPDM INSPECTION
Seams
Seams have been a weak point in EPDM installations for many years. Field experience has shown that joints that are waterproofed during roof installation often fail within the first three years after installation.
They can fail due to application errors or adhesive failure. Cleaning, priming and adhesive application must be done correctly and failure to do any of the three steps can lead to seam failure. The thickness of the adhesive layer is more important than the cleanliness of the surface for creating a permanent bond. However, both are important.
For some new critical occupancy requirements, all field seams (seams created in place) are double sealed by adding an additional strip of membrane over the sealed lap. Double-seal membranes may be covered by an extended warranty.
Because seam adhesives are adversely affected by moisture, EPDM should not be installed over materials with a high moisture content.
Ripples and bulges are sometimes pushed into the seam during installation. Although these seams may be watertight just after installation, they are more likely to fail than seams installed correctly. There are ways to renovate existing seams that are failing.
Roof-wall connection
At roof-wall joints, the EPDM should be extended along the wall beyond the outer covering material.
Change of pitch
When changing the slope of the roof, the EPDM should extend up to the steeper slope.
Brittle Flashing
Older installations may have wall flashings consisting of uncured neoprene instead of cured (vulcanized) EPDM. It was once thought that uncured neoprene would conform to shapes better and vulcanize with exposure to heat and sunlight. Instead, it tends to crack, which appears to be random cracking.
Membrane shrinkage
Membrane shrinkage is a common problem even in recent installations. This can result in tension at the terminations and puckering at the penetrations. This could cause the piping to loosen or crack. Shrinkage can also stress the seams.
The correction consists in cutting the membrane, adjusting it and then patching it with an EPDM strip. This is not something a homeowner can do.
Fasteners extended
Fasteners can back out due to over-tightening during original installation, or loosen from repeated inflation of the membrane under wind loads. The repair involves cutting the diaphragm, replacing the fastener and then patching the diaphragm.
Chemical damage
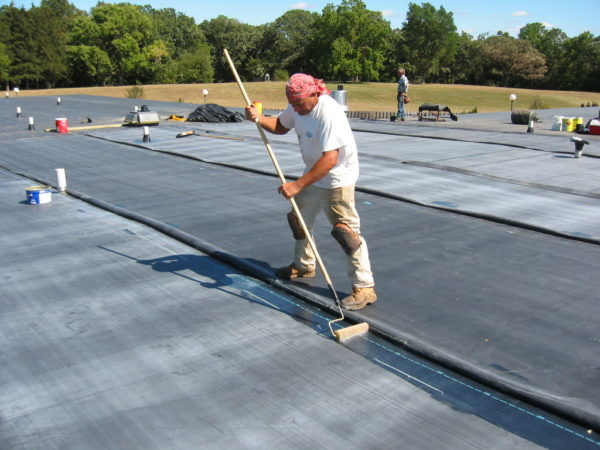
EPDM can be damaged by grease, animal fats, oils and petroleum solvents. Examples of places where these problems can occur are a kitchen exhaust vent and a leak or spill related to a roof-mounted air conditioner.
If there are areas of the roof where any of these conditions persist, have another material installed instead of EPDM.
Coated membranes
To reduce the heat load of the cooling season, EPDM, which is black, is often coated with an energy-reflecting white layer. If the fur is shedding, it needs to be removed, although removal can be difficult and expensive. If peeling is found during inspection, the condition should be assessed by a professional. The evaluation should include contacting the coating manufacturer to confirm that the coating has been designed for long-term compatibility with the membrane.
Ballast Scour
The load can be displaced by wind or waves. It usually appears as a heart-shaped section near the corners of the roof where velocities tend to be highest. The fix is that tiles can be installed, but they require an underlay to prevent abrasion.
A better solution is often larger aggregate applied at 20 to 25 pounds per square foot 10 to 15 feet from the edge of the roof.
Ponding
On low-pitched roofs, water can sometimes collect in low places. This is called thinking. Seams that get wet through immersion can fail. Even when the roof is dry, you can usually spot ponding problem areas by the deposits that collect in them or by the dried rings left behind by evaporated moisture.
Damage caused by foot traffic
Heavy traffic areas are particularly susceptible to damage from abrasion and membrane cutting. This can damage the underlying substrate. These areas should have an additional layer of sacrificial membrane for protection.
Strength of Cuts and Tears
It is difficult to initiate a crack in both reinforced and unreinforced EPDM, but once a crack starts, it propagates relatively easily in unreinforced EPDM. Since tearing is more common with mechanically fastened systems, if you see a mechanically fastened roof with extensive tearing, it may not be reinforced with EPDM.
EPDM is made by a number of different manufacturers and will vary slightly in chemical composition and properties, but generally fails in the ways described above.
Comments